April 08, 2015
The Tip of an Iceberg
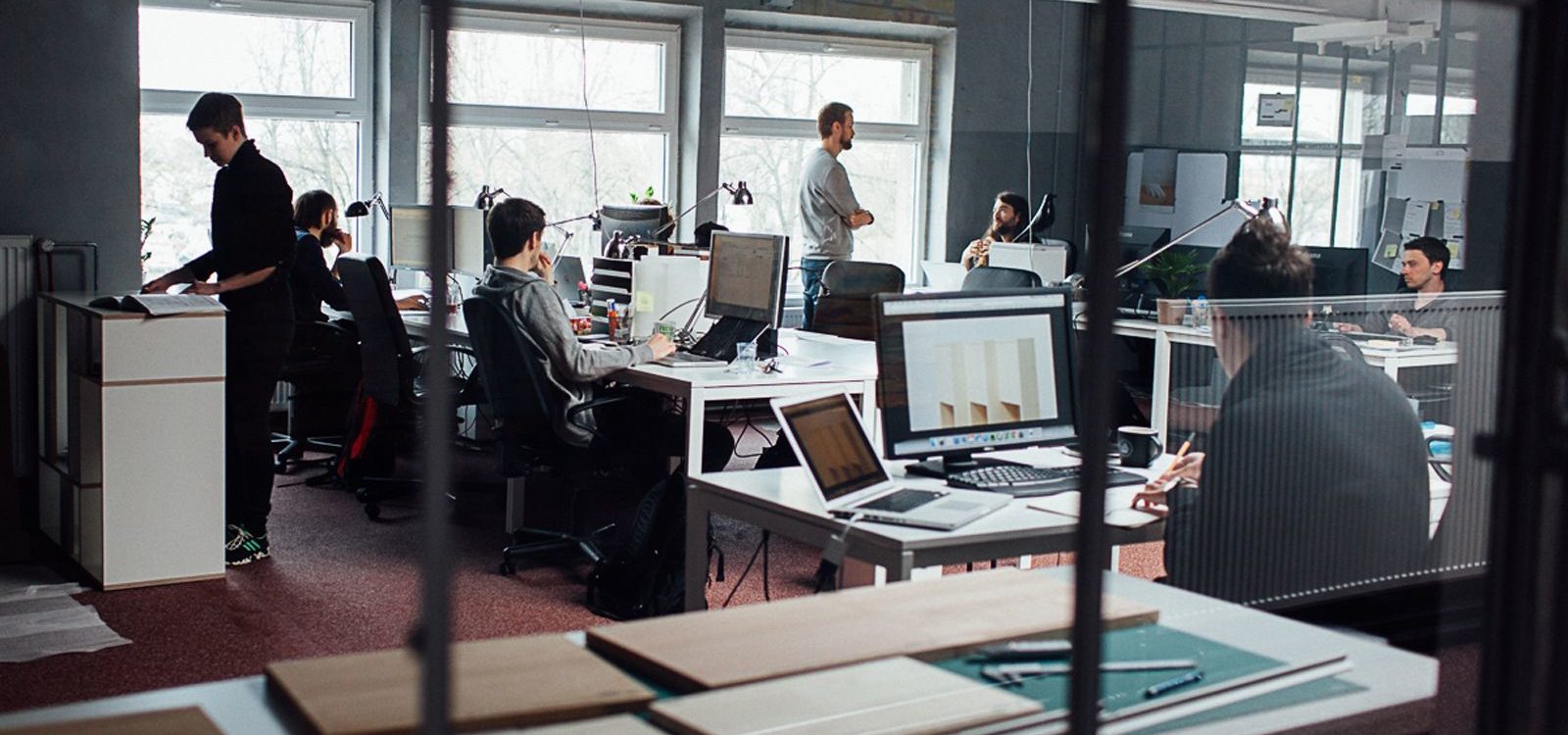
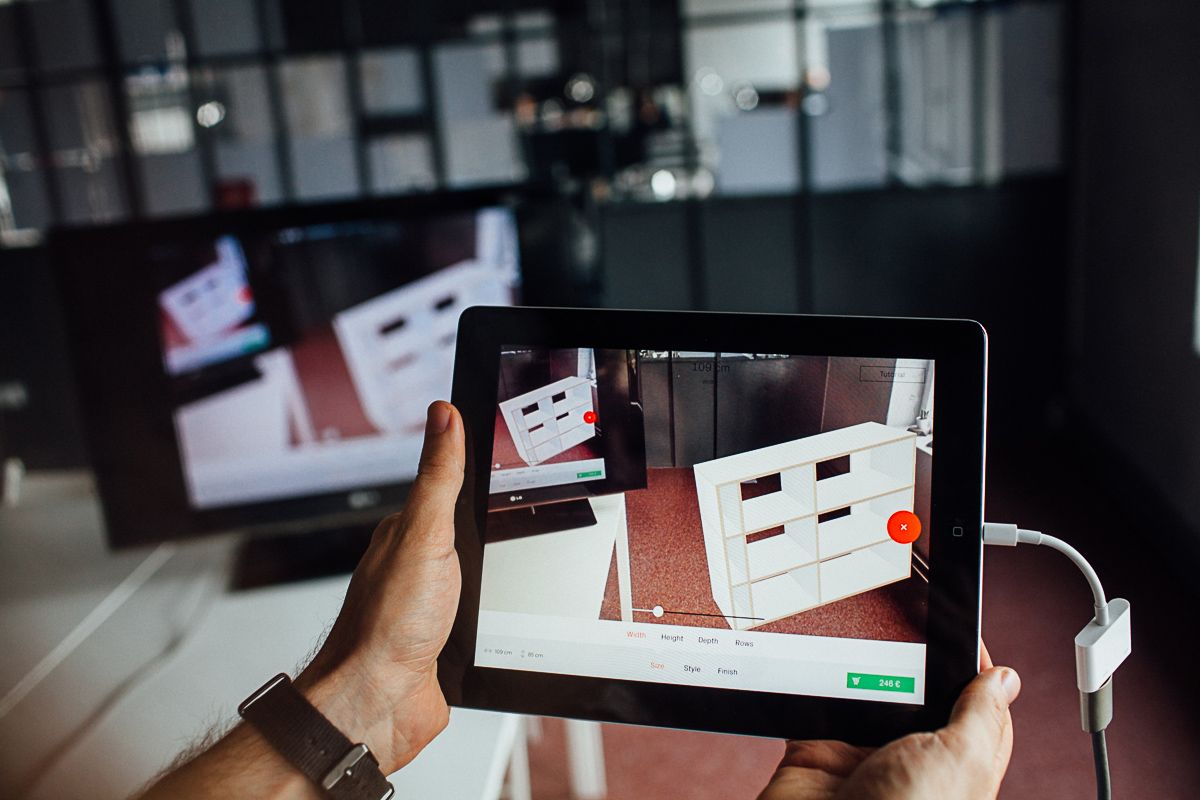
It takes more than one brilliant mind to design and manufacture a customizable piece of furniture. The Tylko design team talks about working on the intersection of technology and design, and pushing the boundaries of what is doable.
Many hands make light work—nowhere is this common truth more on point that at the tylko HQ. It’s here that the ideas for new, customizable products are developed and brought to life, and this task couldn’t be achieved without a tightly knit collaboration. The final product is only the tip on iceberg—beneath hide hours of intensive work from a team that creates innovative solutions on a daily basis. Here, the three people who are the essential links of the product development chain break down the process of designing pieces that are meant to be fluid.
“The distinguishing feature of the way we approach design is that we don’t design a finished product, but a process of creating one, and it’s this process that adds the most value to the final outcome,” says Ewa Kus, parametric designer at tylko. “It’s about offering the user an insight into a designer’s workflow and inviting them to participate on a much deeper level than just changing the color of the laminate.” Ewa has a background in architecture and a flair for coding. After working with tylko’s Head of Parametric Design on a number of projects, she joined the tylko team to turn product ideas into algorithms which determine the user’s engagement.
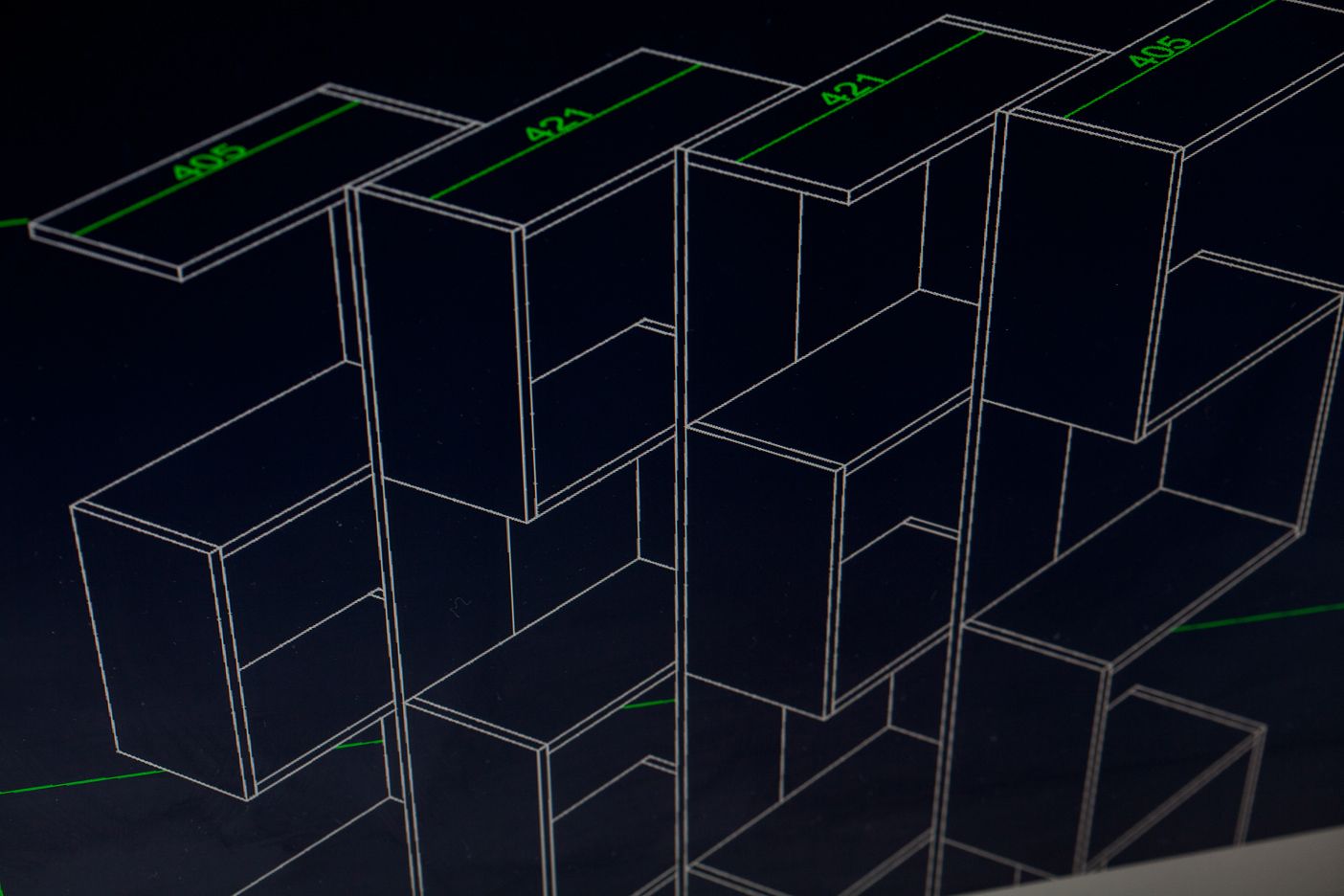
“My job here is to reconcile the design and technology. On the design part, my main goal is to make sure the designer has a good understanding of the possibilities that parametric design offers. I turn a design into a piece of code and advise on making the key decisions: what qualities will be customized and what the spectrum of possibilities will be. The key challenge for both the designer and me is that the piece remains proportionate regardless of the decisions made by the app user.”
“It’s about offering the user an insight into a designer’s workflow and inviting them to participate on a much deeper level than just changing the color of the laminate.”
At tylko, the roles of the designer, parametric designer and engineer are overlapping and blending. A constant feedback loop between the three fields is required to bring the consumers a piece that’s fun and intuitive to customize and easily assembled. Wojtek Tomaszewski, tylko’s product designer admits that this way of working differs from a typical design process. “Before I get to designing, I have to take into account that the final products will have to be made with a technology that enables automatic manufacturing of very different pieces, and will have to be assembled in the same way regardless of their size, material and style. I start by designing several iterations of one piece and very early on consult the design with Ewa to find the possible ways in which the piece could smoothly evolve in 3D. Simultaneously, our engineer Stanislaw advises us on the materials and fittings that will be right for it. There’s a lot trial and error involved because there’s no precedent for customization that goes so deep into the design process,” describes Wojtek.
“There’s a lot trial and error involved because there’s no precedent for customization that goes so deep into the design process.”
Designing a customizable product is hard enough, but getting it made is at least as challenging. There’s no relying on industry standards when the manufacturing process has to be designed anew every time. Tylko’s engineer, Stanislaw Giera describes the constant search for new manufacturing technologies. “The biggest challenge is that it’s not exactly every factory’s dream to make small batches of on- demand products—they’re rather used to working with big furniture companies that order very simple, repeatable products in bulk,” Stanislaw says. However, in addition to the difficulties and challenges, such a specific process opens up many opportunities. “The constant search for innovative manufacturing techniques is also a good source of inspiration for the design itself, and so are material discoveries. Our use of unordinary manufacturing techniques and materials sets us apart from the furniture industry, which is very slow to embrace change.”
Asked about the importance of each stage of the process, Ewa Kus has no doubts. “It’s a collective effort to leave no room for accident and develop a customization process that eliminates the possibility of creating an unattractive piece. That the piece remains buildable at all times is another of my concerns, as I will be the one who writes the software that makes a 3D piece into a set of 2D drawings that will be sent to the factory, so I also need to work closely with the engineers.” The bottom line is obvious but often hard to embrace: you can’t do everything alone.